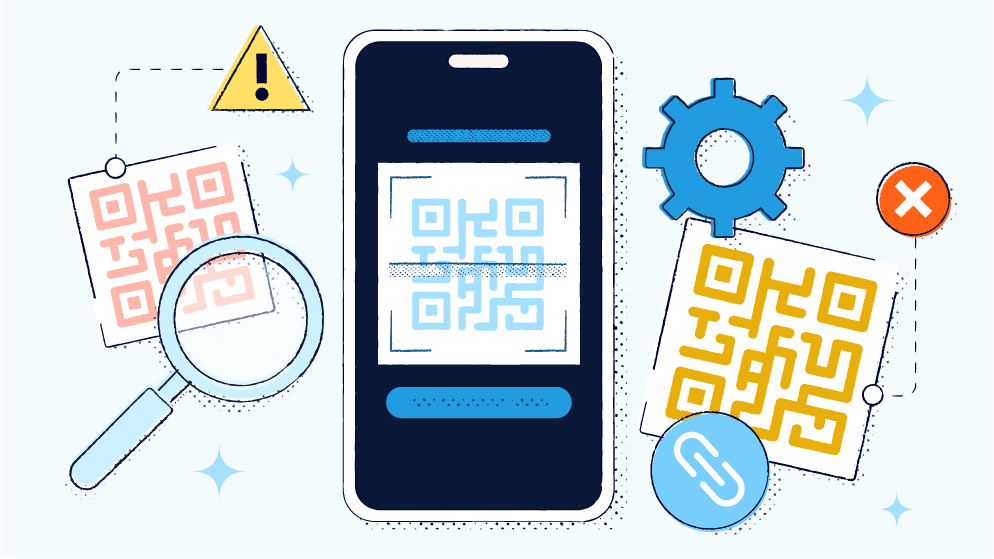
Did you know that Denso Wave—the company that brought us Quick Response Codes—developed them to streamline manufacturing operations? Hard to believe that something virtually every marketing campaign and business uses was first intended for the manufacturing industry, right?
While these pixelated data dots have certainly gone beyond their initial purpose, they remain the gold standard for making manufacturing processes more efficient. Manufacturers today use QR Codes for inventory tracking, asset management, quality control, and more, reducing the risk of making errors and facilitating efficient product and data management.
Want to learn how you, too, can enhance operational efficiency in your processes? Read on as we delve into the whys and hows of QR Codes in manufacturing.
How do QR Codes work for manufacturing processes?
QR Codes can hold a significant amount of information—up to 7,089 numeric characters, 4,296 alphanumeric characters, and 2,953 bytes of data—making them the perfect tools for manufacturers looking to streamline operations by conveying vital product information seamlessly throughout the supply chain. Typically, these characters appear as a series of squares and dots to the naked eye but can be easily decoded with a smartphone camera to reveal the underlying data.
You can link QR Codes to database or spreadsheet URLs carrying a wide range of information to help your team, suppliers, and other members of the supply chain assess product authenticity, origin, quality, and more. Your QR Code URLs can store data types like:
- Product information like manufacturing date and item specifications for efficient product management
- Batch information to help with quality assurance
- Serial numbers to help distinguish products
- Assembly instructions to make tasks easier for workers in the assembly line
- Raw materials and supplier details to enhance transparency in the supply chain
QR Codes vs. traditional barcodes for manufacturing: Which is best?
Let us paint a picture for you—imagine you have hundreds of spare parts to deliver to a client’s warehouse and can pick either a truck or a sedan for delivery. Easy choice, right? The truck is the clear winner as it can handle more product than the sedan, allowing you to complete your delivery in one trip.
QR Codes are the trucks of data dissemination, and traditional barcodes are the sedans—while both can help you transmit vital product information, QR Codes do you one better by allowing you to send more information than would be possible with a 1D barcode. This is because QR Codes store data in both vertical and horizontal axes.
However, information storage capacity isn’t their only selling point—scanners can read them from multiple directions, offering convenience and flexibility in manufacturing processes. And, they can be scanned with mobile devices, eliminating the need for dedicated barcode scanners.
Manufacturers looking for even more flexibility and convenience can adopt Bitly’s GS1 Compliant 2D Barcodes. These are QR Codes with Global Trade Item Numbers (GTINs), often added to product packaging and labels to help companies identify all their items and allow consumers to seamlessly access information like materials used in production and sourcing details.
Examples of how to use QR Codes for manufacturing
From enhancing inventory management in warehouses to facilitating easy information access, QR Codes have become indispensable in manufacturing. Here’s a breakdown of how you can incorporate these nifty innovations into your processes:
Inventory management
QR Codes facilitate efficient inventory management by providing a quick and reliable way to identify and update inventory items. All warehouse staff need to do is scan products as they enter and leave facilities to pull up their pages in your system and allow you to make the necessary updates. This can, in turn, help you adjust production schedules and allocate resources as needed to ensure they meet production demands.
Example in action: You embed QR Codes linked to website or spreadsheet URLs carrying details like serial number and batch information on manufactured products; warehouse staff scans the codes and logs the items into their inventory systems; during order picking or delivery, your staff scans the codes again to pull up the URLs to verify product details—this provides a clear picture of your inventory, limits the risk of making errors during delivery, and expedites the fulfillment process.
Product tracing
QR Codes play a vital role in product tracing. Each QR Code links to a database via URL with unique product identifiers, like product ID, enabling manufacturers to trace their products from warehouses to distribution centers and even final consumers. This allows them to update product status and locations in their systems and enables seamless item recalls, if necessary.
But traceability isn’t only beneficial for manufacturers. It also promotes transparency in the supply chain by helping distributors and customers verify the authenticity of products.
Example in action: Label your products with QR Codes that direct scanners to landing pages containing info such as product IDs, production histories, or verification certificates to allow them to trace the origin of your products. You get real-time updates of every scan, so you can easily determine your products’ locations.
Maintenance or safety information
Machinery or equipment breakdowns and accidents can cause supply chain disruptions and, eventually, downtime, which accounts for losses of up to $260,000 per hour.
QR Codes help manufacturers limit their risk of downtime by providing a seamless way to access database pages and spreadsheets containing equipment maintenance records, repair histories, maintenance schedules, and essential safety information. This way, it only takes a single scan to access all the information needed to keep up with maintenance and ensure workplace safety.
Example in action: Add a unique QR Code to each piece of equipment to lead your team to a landing page containing proper usage guidelines and maintenance records.
Quality control
QR Codes promote seamless quality inspections by allowing manufacturers to identify errors and perform corrective actions quickly. This is vital in maintaining product quality and a positive company image.
Example in action: Use QR Codes linked by URL to quality control reports or checklists for specific batches or products to give quality managers a clear picture of what to look for during inspections and allow them to provide quality assurance feedback seamlessly. You only need to create a spreadsheet containing qualities the managers should look for, encode it in a QR Code, and share the code with your team.
Real-time production updates
When scanned, QR Codes can offer real-time updates on your products’ locations, allowing you to determine their progress status and identify bottlenecks in the manufacturing process or supply chain. This can help with production planning and allow for quick adjustments, enabling you to maintain efficiency.
Example in action: Embed QR Codes on all your products and ask employees to scan them as they move from one stage in the manufacturing or supply chain process to another. The QR Codes can link to spreadsheets that employees can view and update as they work with each item. This gives you a clear visual of where every item is and how long it remains in each stage.
Tips for implementing QR Codes in your manufacturing operations
When used appropriately, a QR Code system can automate your processes and significantly improve manufacturing processes. But, the key word here is “appropriately”—take time to learn how best to leverage QR Code technology before implementing it for optimal results.
Luckily, we’ve got you covered. Here are some tips to guide your QR Code implementation:
Develop a QR Code strategy
Creating QR Codes without a plan is like blindly buying real estate and hoping it’ll appreciate—while it might, it’s more likely that it won’t meet your expectations. Develop a QR Code strategy to guide your actions throughout the implementation process. Here’s what to do for optimal outcomes:
- Assess current processes to identify bottlenecks: Is your greatest problem quality assurance? Or do you need help tracing products across warehouses? Identifying current issues in your manufacturing process will show you what to focus on.
- Set objectives: Base your goals on your pain points—if quality assurance is your main problem, your main objective should be improving quality control.
Use Bitly to create and manage your QR Codes
Bitly’s QR Code Generator is one of the best solutions for manufacturers looking to enhance operational efficiency, as it’s not only easy to use but also allows you to manage your codes and view scan analytics, all from a single dashboard. To make QR Codes using Bitly:
- Log in to your account.
- Select Create new and tap QR Code.
- Enter your destination link in the Destination URL field.
- Tap Design your code to choose your preferred QR Code style, colors, and logo.
- Select Create your code.
- Download your code.
You can easily redirect your QR Codes to new destinations, allowing you to use the same codes for different purposes. For example, to help quality managers with quality control, you can create a Bitly QR Code linked to inspection checklists and later redirect the same code to product information to help distributors and consumers access relevant information, all from your Bitly account.
You can also access scan metrics, like scan by location and scan by day, allowing you to follow your products’ journey throughout the manufacturing process. With location and time tracking data, you can quickly identify problem areas and take appropriate actions to boost efficiency.
Use common QR Code best practices
You can maximize the benefits of integrating QR Code technology into your workflows by following best practices like:
- Ensuring proper QR Code placement: Position your QR Codes somewhere your audience can easily see and scan them, for example, on product packaging.
- Choosing an appropriate size: Ideally, the QR Code should be at least 2 cm x 2 cm (.8 in x .8 in), or one-tenth of the intended scanning distance.
- Using contrasting colors: You can use the typical black and white or choose other colors, as long as they have a high contrast for optimal scannability.
- Training your staff: Teach employees how to scan QR Codes, manage them, and track their analytics for a smooth process.
Integrate with existing systems
Integrate your QR Code system with existing manufacturing and inventory solutions to minimize disruptions and leverage the full potential of all systems. Most systems are designed to handle QR Code technology, so this should be relatively straightforward for professionals. Work with IT and software development teams for optimal outcomes.
Keep the QR Code content up-to-date
Outdated content is a liability for your business as it can cause inefficiencies or confusion in the manufacturing process. To prevent this, regularly update your QR Code content, ensuring scanners get the most accurate, relevant, and up-to-date information.
Your ability to do so will depend on your choice of QR Codes. You typically have two options: Static and Dynamic QR Codes. Dynamic QR Codes, which is what Bitly offers, are the best option for manufacturing processes, as they allow content changes. And, with Bitly’s easy-to-use platform, updates are a breeze. You simply need to find the code you want to update and redirect it to your new destination.
Use QR Codes to craft the next chapter in manufacturing
Integrating QR Codes into your manufacturing process can streamline operations, provide easy access to information, reduce errors, and help expedite production and delivery. To successfully implement the technology, develop a clear strategy based on your main pain points and find a reliable QR Code generator, like Bitly.
With Bitly, you can forget about manual data entry errors, ineffective product tracking systems, and poor inventory management. You get access to an easy-to-use, robust, and scalable platform that allows you to create a wide range of QR Codes, manage their destinations, and assess their scan data to improve manufacturing operations even further.
Get started with Bitly today to streamline complex processes and boost your business’ operational efficiency.